What is TFT-LCD? TFT-LCD is the abbreviation of Thin-Film Transistor Liquid-Crystal Display (Thin-Film Transistor Liquid-Crystal Display) How does TFT-LCD light up? Simply put, a TFT LCD display can be regarded as a layer of liquid crystal sandwiched between two glass substrates. The upper glass substrate is combined with a color filter, while the lower glass is embedded with transistors. When the current passes through the transistor, the electric field changes, causing the liquid crystal molecules to deflect, thereby changing the polarization of the light, and then using the polarizer to determine the light and dark state of the pixel. In addition, the upper glass is laminated with the color filter to form each pixel (Pixel) that contains three colors of red, blue and green. These red, blue and green pixels form the image on the panel. The three main processes of TFT-LCD: The three main processes: Front Array The front Array process is similar to the semiconductor process, but the difference is that thin film transistors are made on glass instead of silicon wafers. Middle Cell The cell in the middle section is the glass substrate of the previous Array, combined with the glass substrate of the color filter, and liquid crystal (LC) is poured between the two glass substrates. Module Assembly Back-end Module Assembly The back-end module assembly process is the production operation of assembling the glass after the Cell process with other components such as backlight boards, circuits, and outer frames.
TFT manufacturing principle and simple manufacturing process
The main three-stage process of TFT-LCD:
The first is the front Array
The Array process in the previous part is similar to the semiconductor process, but the difference is that thin film transistors are fabricated on glass instead of silicon wafers.
Then the middle cell
The Cell in the middle section is the Array glass of the previous section as the substrate, combined with the color filter glass substrate, and liquid crystal (LC) is poured between the two glass substrates.
Finally, the latter part of the Module Assembly (module assembly)
The assembly process of the back-end module is to assemble and produce the glass after the Cell process and other components such as circuits, frames, backlights and so on.
1. Array manufacturing process (array)
1) A piece of glass with a smooth surface and no impurities is the most important raw material for making TFT glass substrates. Before making, you need to wash the glass clean with a special detergent, then dehydrate and spin dry.
2) To coat the glass substrate with a metal film, the metal material needs to be placed in the vacuum chamber, and after the special gas on the metal generates plasma, the atoms on the metal will be knocked against the glass, and then a layer of layers will be formed. Metal film too.
3) After the metal film is plated, we also need to plate a non-conductive layer and a semi-conductive layer. In the vacuum chamber, the glass plate is heated first, and then a special gas is sprayed by a high-voltage sprayer to let the electrons and the gas Plasma is generated, and after a chemical reaction, a non-conductive layer and a semiconductor layer are formed on the glass.
4) After the film is formed, we need to make the pattern of the transistor on the glass. First, enter the yellow light room and spray the photoresist with extremely high sensitivity, then put on the photomask to irradiate the blue-violet light for exposure, and finally send the developer to the developing area to spray the developer, which can remove the photoresist after the light and let the light The resist layer is shaped.
5) After the photoresist is shaped, we can perform wet etching with etching to expose the useless film, or dry etching with the chemical reaction of plasma. After etching, remove the remaining photoresist with liquid, and finally Generate the circuit pattern needed for the transistor.
6) To form usable thin-film transistors, it is necessary to repeat the process of cleaning, coating, photoresist, exposure, development, etching, and photoresist removal. Generally speaking, to manufacture TFT-LCD, it is necessary to repeat 5 to 7 times.
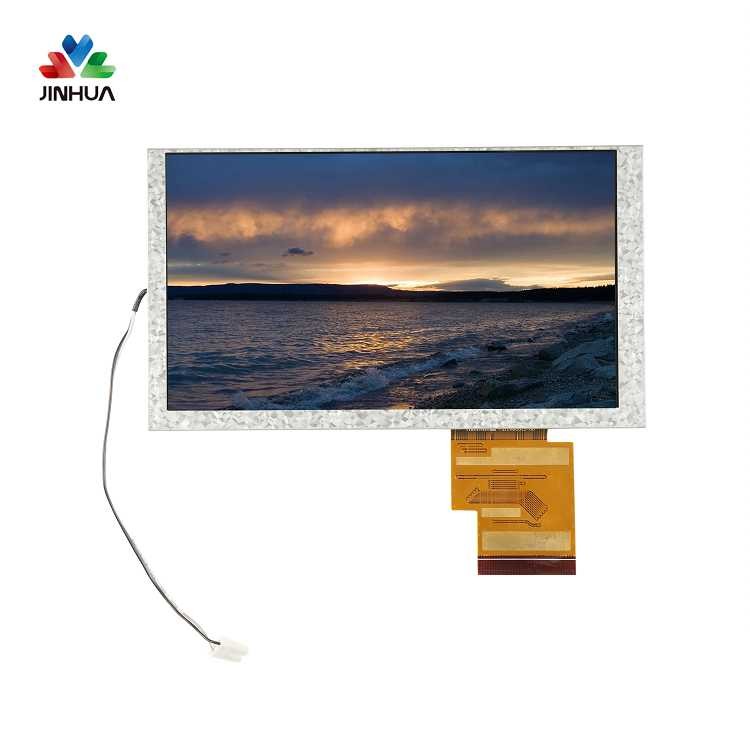
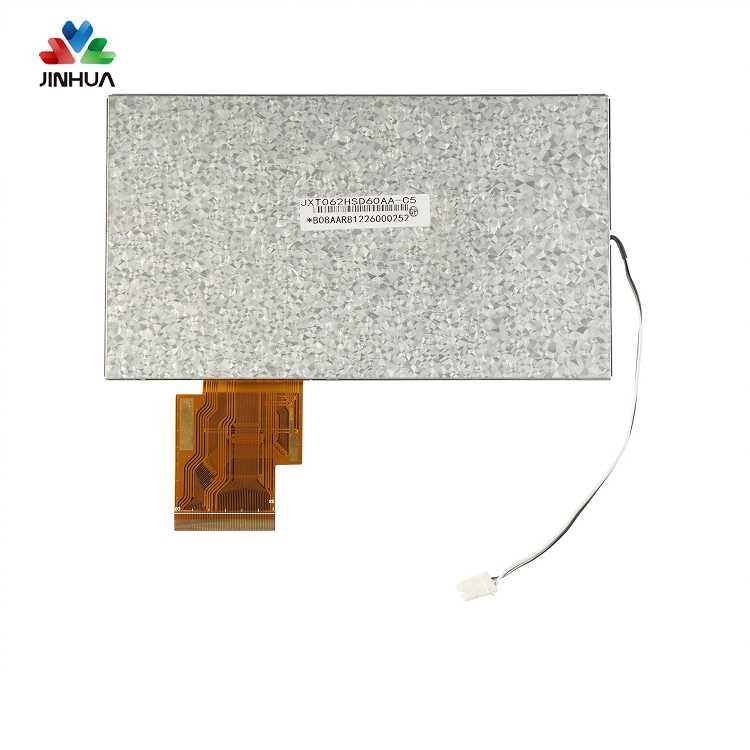