LEDs are characteristic-sensitive semiconductor devices and have negative temperature characteristics. Therefore, they need to be stabilized and protected during the application process, which leads to the concept of driving. LED devices have almost harsh requirements for driving power. Unlike ordinary incandescent bulbs, LEDs can be directly connected to 220V AC mains. The LED is driven by a low voltage of about 3 volts. It is necessary to design a complicated conversion circuit. LED lights for different purposes must be equipped with different power adapters. In the international market, foreign customers have very high requirements on the efficiency conversion, effective power, constant current accuracy, power supply life, and electromagnetic compatibility of the LED drive power supply. The design of a good power supply must take these factors into consideration, because the power supply is in the entire luminaire. The function is as important as the human heart.
Analysis of several common LED screen module driving methods
Due to the limitation of the power level of the LEDs, it is usually necessary to drive multiple LEDs at the same time to meet the brightness requirements. Therefore, a special drive circuit is required to light the LEDs. At present, the mainstream LED driving methods are as follows:
RC step-down
Use the impedance of the capacitor under AC to limit the input current, so as to obtain a DC level to power the seven segment LED display. This kind of driving method has a simple structure and low cost, but the input is not isolated, which has potential safety hazards. Moreover, the conversion efficiency is very low, and constant current control cannot be achieved.
Isolated flyback circuit
Using a flyback circuit, a DC level is generated on the secondary side through a transformer, and then the ripple of this level is fed back to the primary side through an optocoupler, so that the self-excitation is stable. This type of circuit meets the requirements of safety regulations, and the output constant current accuracy is better, and the conversion efficiency is higher. However, due to the need for optocouplers and secondary-side constant current control circuits, the system is complicated, bulky, and costly. It has been gradually replaced by the original plan.
Original side plan
The primary side solution is to control the output power and current completely on the AC primary side, the most accurate can achieve 5% constant current accuracy, and the secondary side only needs a simple output circuit. The primary side mainly relies on the feedback of the auxiliary side to control the output voltage, relies on the current limiting resistor to control the primary side current, and at the same time multiplies the turns ratio to control the accuracy of the output current. The original-side solution inherits the various advantages of the isolated flyback circuit, while the structure is simple, and it can achieve small size and low cost. It has become the mainstream driver at present.
The problem of constant current accuracy of the primary side: The production accuracy of the transformation is difficult to control, resulting in a large output current drift when the primary side solution uses a low-quality transformer. Therefore, the primary side solution has been improved to increase the secondary side constant current control circuit, which is more complicated than the ordinary primary side solution, but compared with the flyback solution, the optocoupler can still be omitted, and the system has the highest cost performance.
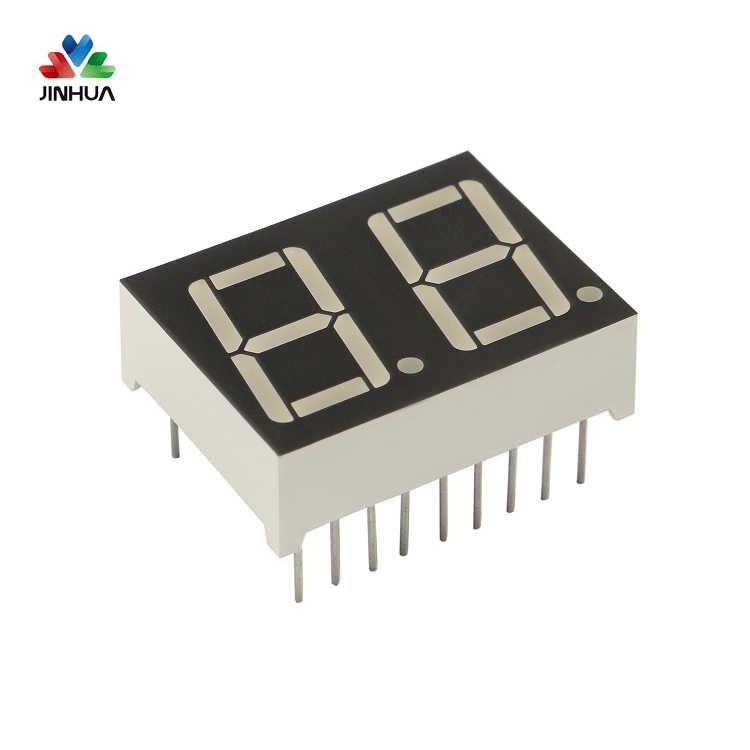
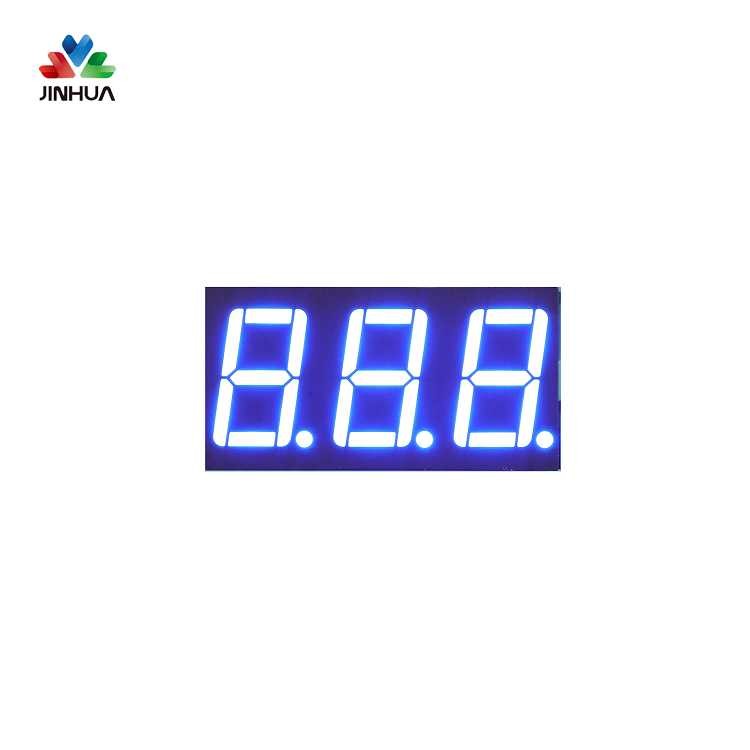
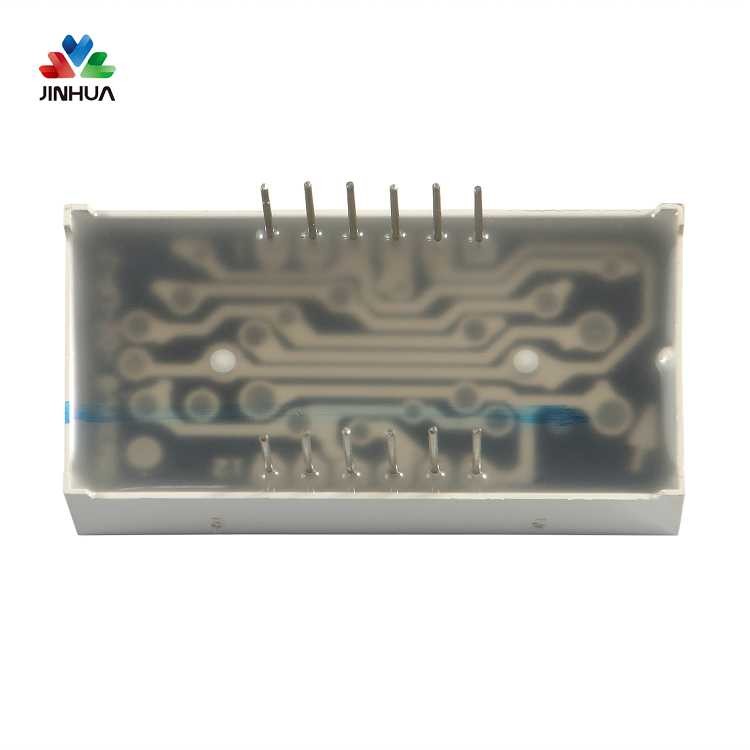